Installation manual of refractory rotary kiln
Jun 10,2014
Preparation for Installation
1,Study the drawings carefully to understand the design intentions and to find out the design requirements and main points for each part. According to specific installation task, work out the project's schedule, cross operation plan and response plan in dealing with possible fault or accident.
2,Make a good preparation in technology and in material for the installation to meet the design requirements. Make sure the equipment installation and the kiln lining installation run smoothly and achieve best quality.
3.Check carefully the construction site to make sure the variety, specification, quantity and quality of the materials, tools and supporting facilities on the site can meet the construction requirements and persons and organizations to participate in the installation are confirmed.
4.Make sure the kiln is cleaned up, kiln shell is undeformed, weld seams and joint are smoothed, and brick retaining rings are squared with the kiln axis.
Notices for bricklaying
1,Make sure the brick lining and kiln shell or rotary drum cooler are homocentric reliably. It is required that four corners of bricks' cold face are made "touch the ground" (the top of the brick is set close to the kiln shell to avoid possible leak). On the inside of brick lining of each ring, every brick should fully contact with the wege of its adjacent brick to avoid stress concentration that may lead to local brick lining failure.
2,Lock in the brick lining to ensure the brick lock zoon is not the weakest link of the kiln lining.
3,Steel plate should be used as limited as possible. Steel plate used in locking gap should be applied dispersedly to avoid an oxidation of the steel plate, as the accompanied volume expansion would otherwise tighten adjacent bricks to caurse cracking or peeling off.
4,In the installation of the l//inings of preheater, decomposing furnace, kiln gate hood and other immovable parts, the brick joint thickness ranges from 1 to 1.5mm and the joints should be fully filled with mortar. Lining surface should be smooth without steps.
5.Spacing between the basic brick rings may embed paperboard as expansion gaps to counterbalance the compressive stress.
6. Refractory mortar is usually used for the installation of high alumina bricks and alkali-resistant bricks. The mortar must be fully filled in the brick joints.
7, During the construction process, make sure to use flexible tools such as wooden, rubber or rigid plastic hammer or mallet. Hitting refractory brick with rigid hammer is absolutely forbidden.
Installation Method
1,Arch law laying brick, as figure 1 shows, is usually applied in large kiln with a diameter over 4m. as figure 1 shows.
2, Top support law laying brick is usually applied in small and medium kilns with diameters less than 4m. Two supports called crossing top support, as figure 2 shows, will be used during the lining installation in kilns with a diameter more than 3.6m. Only one support called beeline-shaped top support, as shown in figure 3, is needed in kilns with a diameter less than 3.6m.
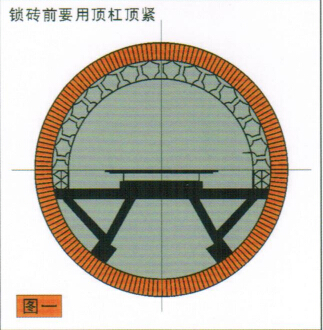
Heating-Up
After the overhaul, the heating-up quality is vital. During the heating-up process, the principle of "slowly heating up and never dropping back" must be obeyed to avoid lining burst or hot spot phenomenon and to enhance the kiln lining' s durability.
During heating-up process, it is very important and necessary for the kiln to rotate from intermittently to continuously and from low speed to normal speed. This can help maintan good temperature homogeneity of lining surface and avoid kiln centerline deviation, local elliptical degree enlargement and kiln body deformation.
Notes for overhaul
When closing down the kiln, the lining must be gradually cooled down following proper rule of temperature reduction to avoid the damage of the hot face of brick lining due to otherwise fast cooling. For the new dry-process cement kiln, natural cooling for 24h must be ensured after shuting down the kiln, then the kiln gate can be opened to accelerate cooling. It is also necessary for traditional kiln to adopt slow cooling until kiln crust and kiln lining turning black before rapid cooling applies.
Safe cooling precautions are recommended as follows:
1,Shut down the decomposing furnace system 1-2 hours before closing down the furnace. Close the gate of exhaust fan before shuting down the kiln system. The exhaust fan' s gate is closed while dust catcher should not be shut down so as to remain dust catcher pulling wind tenderly.
2.Rotating speed of the kiln will be 360cper 45 minutes during the first 24 hours, while in the next 24 hours the rotating speed will be decrease to 360°per 90 mimutes.
3.Primary air amount should be decreased to 10% of flow capacity.
4,Open the kiln gate to hasten cooling after the kiln has been closed down for 24 hours.